- Es la aportación de NI-P, Ni-B y Ni-PTFE mediante la reducción catalítica de iones de níquel.
- No es necesario el paso de corriente eléctrica.
- Temperatura de trabajo de 90+/- ºC.
- Es preferible niquelado a toda la pieza que zona selectiva.
- Capa de deposición de 1 a 300µ.
- Dureza de 500HV a 950HV (con un tratamiento térmico).
- Industrias de alimentación
- Electrónica
- Petroquímica
- Instrumental médico-quirúrgico
- Aeronáutica
- Ferrocarriles
- Energía nuclear
- Determinados moldes de plástico
- Industria militar
- Industria química
- Industria del automóvil
- Industria neumática e hidráulica
- Otros
- Resistencia a la corrosión
- Control preciso de capa
- Uniformidad de la capa
- Dureza de 500-950Hv
- Resistencia a la abrasión
- Bajo coeficiente de rozamiento
- Protección contra el desgaste y gripado
- Resistencia a tensiones de compresión
- Se puede realizar depósito magnético / no magnético
- Conductividad
- Fácil soldabilidad
- Buena lubrificación
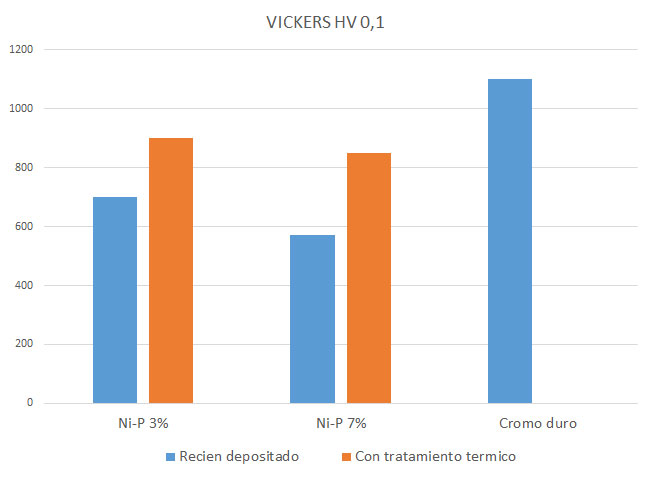
Alcalis, ácidos con pH>5, compuestos orgánicos e inorgánicos y oxidantes.
Ácido nítrico, ácido crómico, ácido clorhídrico, ácido monocloroacético, ácido fosfórico, cloruro de sodio, cloruro de bario, clorhidrato de anilina, sulfato amónico, hipoclorito y sosa al 72% + mercurio.
- Baño de bajo contenido en fosforo (1-4% P)
- Baño de medio contenido en fósforo (4-9% P)
- Baño de alto contenido en fosforo (10-14% P)
- Baño de níquel con composite
- PTFE
- Carburo de silicio
- Diamante
- Nitruro de Boro
- Buena resistencia a la abrasión
- Buena resistencia a la erosión
- Menor adherencia a espesores superiores a 10µ
- Resistencia a la corrosión moderada
- Soldabilidad perfecta a bajos espesores (3-4µ) con electrodo de plata o plomo estaño magnético
- Buena resistencia a la abrasión
- Buena adherencia sustrato-película
- Resistencia a la corrosión moderada
- Buen comportamiento de elongación
- Aquellos depósitos con un contenido >8% en P no son magnéticos, a no ser que se sometan a un tratamiento térmico
- Alta resistencia a la abrasión
- Buena resistencia a la elongación
- Depósito poco tensionado (buena adherencia)
- Depósito no magnético inclusivo a temperaturas de 275ºC
- Se pueden conseguir espesores elevados (mayores a 300µ) que, expuestos a un tratamiento térmico de 385ºC, presentan una buena adherencia con el sustrato
- Consiste en la incorporación de partículas ocluidas en una proporción del 20-25% en volumen en sus depósitos uniformemente distribuidas en toda la matriz
- Las partículas confieren al depósito propiedades especificas en función del composite elegido
- El Níquel PTFE es el más utilizado por sus propiedades lubricantes y antiadherentes
- En cambio, el composite de carburo de silicio y diamante se utilizan para mejorar la resistencia al desgaste
- El composite de nitruro de boro codepositado en una matriz de níquel de bajo a medio contenido en fósforo, las partículas de nitruro de boro pueden soportar hasta 3000ºC (teniendo en cuenta que el punto de fusión de la matriz de níquel es de 890ºC)
Probeta de acero pulido, con espesor de 25µ, sin tratamiento térmico.
- Niquel químico en bajo contenido en P…….. 35h de niebla salina/acética
- Níquel químico en medio contenido en P……75h de niebla salina/acética
- Níquel químico en alto contenido en P………150h de niebla salina/acética
La deposición del níquel es completamente uniforme y al ser auto catalítica el recubrimiento se realiza en toda la superficie. Es preferible el niquelado de toda la pieza a una niquelado selectivo ya que la protección debe ser perfecta y se producirá un resalte y no un difuminado entre la zona con recubrimiento y la zona sin recubrimiento.
La adherencia del niquelado químico esta sujeta al estado superficial de la pieza, a la preparación previa, a los turnovers del baño de níquel químico y al mantenimiento exacto de los valores de las sales y catalizadores del baño.
Turnover es el concepto por el cual se define la reposición en productos del baño inicial. A medida que el baño trabaja, el baño va envejeciendo y aumentado la cantidad de ortofosfito, alterándose el brillo (cada vez es más apagado), la cantidad de P, la dureza y la adherencia.
En general la vida útil del baño de níquel se encuentra entre los 5 y 8 turnovers máximo. En función de sustrato y las características que se quieren obtener del niquelado se trabajará dentro de una franja de turnovers determinados (por ejemplo: en el caso de Aluminio brillante, no es recomendable trabajar más allá del tercer turnover)
Al realizar un tratamiento térmico, la estructura del níquel químico pasa de amorfa a cristalina. Se mejora la adherencia de la capa al sustrato, su dureza. Pero, según el material base, la resistencia a la corrosión puede disminuir un 40%.
En el caso de que se realice una operación de tratamiento térmico en las piezas que anteriormente a la fase de niquelado hayan sido sometidos a otro tratamiento, puede que se produzca un revenido y, por consiguiente, se disminuya la dureza de la pieza.
La adherencia del níquel químico, aún siendo muy buena, tiene un mayor riesgo de desprendimiento en las aristas, donde un golpe puede hacer saltar una porción de níquel. Es por ello que las operaciones de rectificado o mecanizado después del niquelado deben realizarse con mucho cuidado.
- Deposición uniforme
- Recubrimiento a toda la pieza, en todas sus zonas, sin presencia de acumulaciones
- Aumento de capacidad de producción
- Aceros aleados
- Aceros al carbono
- Aceros cementados
- Aceros templados
- Aceros nitrurados
- Acero inoxidable
- Aluminio
- Cobre
- Bronce
- Fundición de hierro
- Hierro
- Latón
- Niquel